Ground surface friction
Ground surface friction
Hello,
Are there currently any plans ( or is it even possible) to improve on the current ground friction physics? After some googling I found an adjustment made through FSUIPC (I think) but that looks like it doesn't work with the current version of P3D.
Ground friction is quite high and unrealistic. Single engine taxiing is also practically useless as you will end up using more fuel than saving.
Does anyone know of a way to tweak the ground friction in P3D 4.4?
Are there currently any plans ( or is it even possible) to improve on the current ground friction physics? After some googling I found an adjustment made through FSUIPC (I think) but that looks like it doesn't work with the current version of P3D.
Ground friction is quite high and unrealistic. Single engine taxiing is also practically useless as you will end up using more fuel than saving.
Does anyone know of a way to tweak the ground friction in P3D 4.4?
Re: Ground surface friction
I checked the PMDG777 (two engines) all ok here.Ph_737NG wrote: ↑Mon Feb 04, 2019 4:57 am Hello,
Are there currently any plans ( or is it even possible) to improve on the current ground friction physics? After some googling I found an adjustment made through FSUIPC (I think) but that looks like it doesn't work with the current version of P3D.
Ground friction is quite high and unrealistic. Single engine taxiing is also practically useless as you will end up using more fuel than saving.
Does anyone know of a way to tweak the ground friction in P3D 4.4?
Best Regards,
Vaughan Martell PP-ASEL (KDTW)
Vaughan Martell PP-ASEL (KDTW)
Re: Ground surface friction
I probably should have been a little more specific. I’m not having trouble taxiing on two engines. I’m speaking of how realistic the ground friction is. For example in the real world I have never flown a jet that wouldn’t taxi at idle thrust. You obviously need some break away thrust in many cases but, In P3D at idle thrust you will come to a stop. On top of that the real aircraft I have flown ALL taxi on a single engine quite well. In P3D you sometimes need 70%+ N1 just to get moving and after that require much higher than idle thrust to keep moving. Now there are some areas in the real world that could be slightly realistic (e.g. taxiway C in LAX westbound, is slightly uphill and takes a little bit more to get moving on a single engine) but slopes are not simulated in P3D. Additionally while taxiing single engine it requires quite a lot of rudder to stay moving straight. All of which are not issues in real aircraft.
Re: Ground surface friction
I did a quick test.P3Dv4.4Ph_737NG wrote: ↑Mon Feb 04, 2019 4:55 pm I probably should have been a little more specific. I’m not having trouble taxiing on two engines. I’m speaking of how realistic the ground friction is. For example in the real world I have never flown a jet that wouldn’t taxi at idle thrust. You obviously need some break away thrust in many cases but, In P3D at idle thrust you will come to a stop. On top of that the real aircraft I have flown ALL taxi on a single engine quite well. In P3D you sometimes need 70%+ N1 just to get moving and after that require much higher than idle thrust to keep moving. Now there are some areas in the real world that could be slightly realistic (e.g. taxiway C in LAX westbound, is slightly uphill and takes a little bit more to get moving on a single engine) but slopes are not simulated in P3D. Additionally while taxiing single engine it requires quite a lot of rudder to stay moving straight. All of which are not issues in real aircraft.
PMDG-777 Not fully loaded (Gross Weight - screenshots) with my setup (Saitek throttles calibrated in FSUIPC).
KDTW 4R
N1 idle 21.7
N1 taxi 24.2
Once I start rolling then going back to idle it takes a good distance to come back to a stop. I would have normally applied brakes after reducing to idle e.g. to hold short.
All ok for my useage.
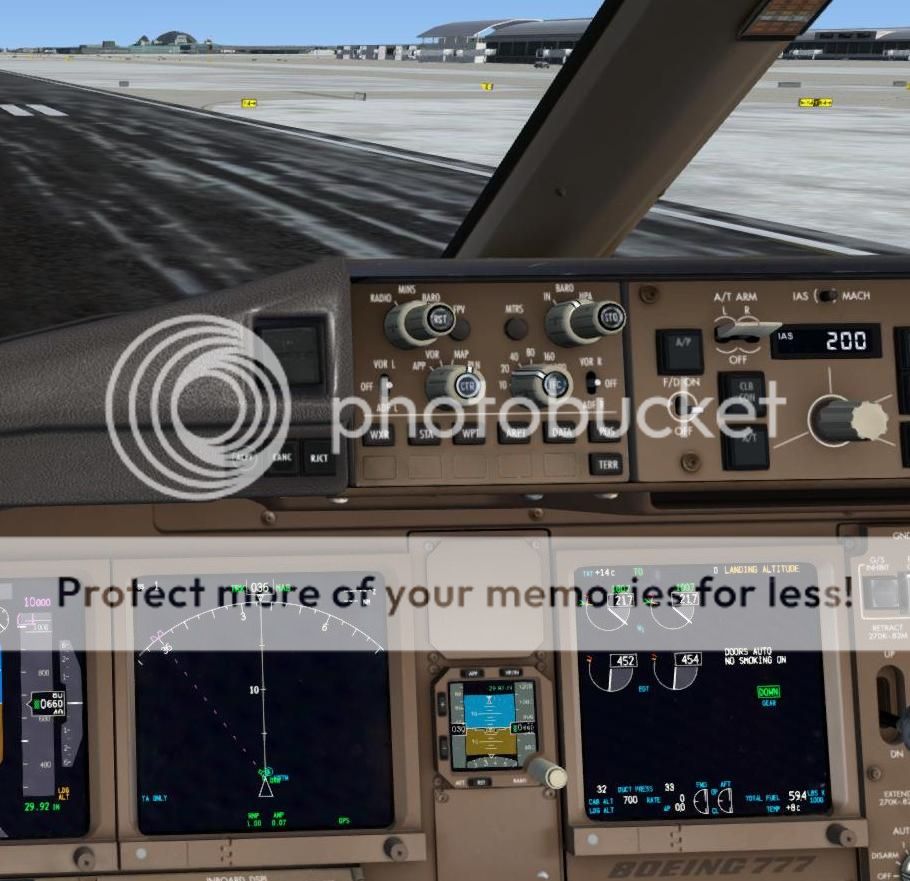
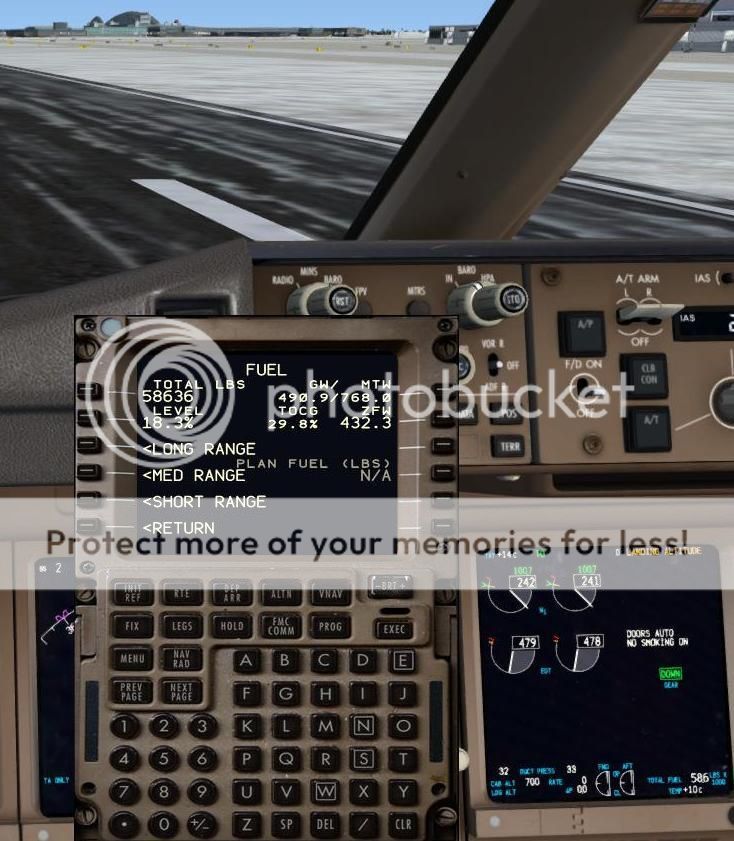
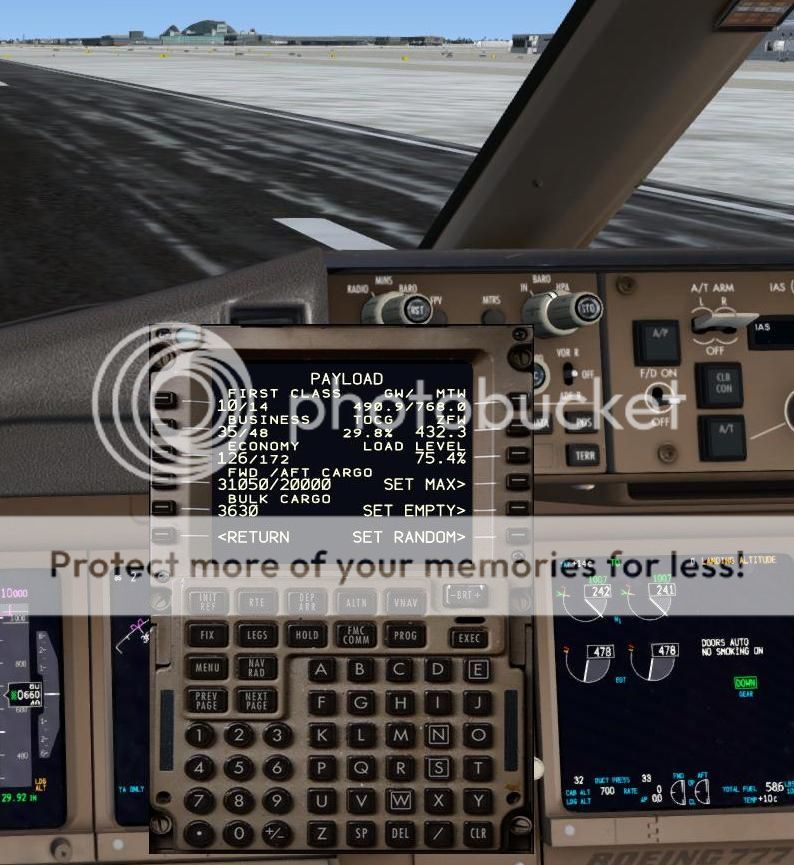
Best Regards,
Vaughan Martell PP-ASEL (KDTW)
Vaughan Martell PP-ASEL (KDTW)
Re: Ground surface friction
The "ground surface friction" modeled in P3D and ESP/FSX/FS9 before it is a very simple example of how to build an arcade game. The problem is not complex for a mechanical engineer and it has little to do with friction unless you are in a skid at which point you broke contact are now sliding and now friction comes into play. What is required is a model that incorporates "rolling resistance," which varies wildly based on tires size, number, inflation, wall stiffness and weight. This kind of simulation is probably beyond the scope of what LM is trying to achieve here and I wouldn't expect it. Ever.
PMDG in their QOTSII B747 product has worked outside of the box and used their own modeling for rolling resistance. The difference is hard to compare to other aircraft simply because of it's size and weight but it's good to see product developers extending the craft.
PMDG in their QOTSII B747 product has worked outside of the box and used their own modeling for rolling resistance. The difference is hard to compare to other aircraft simply because of it's size and weight but it's good to see product developers extending the craft.
Dan Downs
KCRP
KCRP
Re: Ground surface friction
Any idea what specific changes PMDG made to change this on their 747? I'd like to be able to make my own adjustments if need be to make it work at least somewhat more realistically.downscc wrote: ↑Tue Feb 05, 2019 4:32 pm The "ground surface friction" modeled in P3D and ESP/FSX/FS9 before it is a very simple example of how to build an arcade game. The problem is not complex for a mechanical engineer and it has little to do with friction unless you are in a skid at which point you broke contact are now sliding and now friction comes into play. What is required is a model that incorporates "rolling resistance," which varies wildly based on tires size, number, inflation, wall stiffness and weight. This kind of simulation is probably beyond the scope of what LM is trying to achieve here and I wouldn't expect it. Ever.
PMDG in their QOTSII B747 product has worked outside of the box and used their own modeling for rolling resistance. The difference is hard to compare to other aircraft simply because of it's size and weight but it's good to see product developers extending the craft.
Re: Ground surface friction
They took the ground rolling resistance effect outside of P3D and use their own code to provide the simulation. This is not something a user can do, there are no tweaks or settings to provide this.
Dan Downs
KCRP
KCRP
Re: Ground surface friction
I agree that the ground friction needs to be adjusted. Taxiing could be much more realistic.
PMDG did a good job with the latest 747. Also FSPS : Frictionality proves that this can be universally adjusted, but is available in P3D V3 and FSX only.
Surly LM can make a universal adjustment, as default, in V4 and moving forward. A cfg entry would be ideal (if possible) so users can adjust as they see fit; everybody could be happy.
PMDG did a good job with the latest 747. Also FSPS : Frictionality proves that this can be universally adjusted, but is available in P3D V3 and FSX only.
Surly LM can make a universal adjustment, as default, in V4 and moving forward. A cfg entry would be ideal (if possible) so users can adjust as they see fit; everybody could be happy.
Win 10 Pro 64bit | ROG MAXIMUS XII HERO | i9 10850K |DDR4 3600MHZ G.SKILL TRIDENT Z NEO- 128GB | 1200W PLATINUM POWER SUPPLY | RTX 3090 |Samsung 970 evo plus 2TB NVME | 2nd M.2 Solid State 2TB | Seagate IRONWOLF PRO 8TB | DEEPCOOL CASTLE 240EX
Re: Ground surface friction
@adambreed
@robmcarthy
Please please consider this, even if you alter the PDK to allow developers to better model ground handling!
Blessings
Duncan Odgers
@robmcarthy
Please please consider this, even if you alter the PDK to allow developers to better model ground handling!
Blessings
Duncan Odgers
Re: Ground surface friction
The original default values contained in SIM1.DLL are the issue, I have done a lot of research on friction coefficients and posted my findings on fsdev. The bottom line here is that using the default rolling friction sim value for concrete causes other values within the airfile to become skewed. All of the airfiles available today are made to overcome this incorrect value with side effects.
The high default rolling friction value causes the turbine tables to be skewed to overcome high friction, one must set high Fn (net thrust) in 1506 for the idle/static mach line. This higher unrealistic Fn value causes fuel burn to be higher at idle because FB is proportional to thrust. Some developers then overcome this high FB part by faking the fuel burn gauge to display the correct FB bypassing the sim variables.
I have experimented a lot here and set up an airfiles turbine tables to exactly match the real GE90-94b. I know the thrust values (at ISA and ZFWs) to get the aircraft rolling and also have a thrust to CN1 table. I concluded that the sim1.DLL values are approximately treble the real world values for concrete (0.014).
Its not just the rolling friction coefficients, the sliding is wrong also which is why aircraft skid in turns whilst taxiing.
The problem for LM here is that if they fix sim1.dll, they break every other legacy airfile. Its not a big job to fix the airfile, but I suspect commercial developers would rebel against this !
The high default rolling friction value causes the turbine tables to be skewed to overcome high friction, one must set high Fn (net thrust) in 1506 for the idle/static mach line. This higher unrealistic Fn value causes fuel burn to be higher at idle because FB is proportional to thrust. Some developers then overcome this high FB part by faking the fuel burn gauge to display the correct FB bypassing the sim variables.
I have experimented a lot here and set up an airfiles turbine tables to exactly match the real GE90-94b. I know the thrust values (at ISA and ZFWs) to get the aircraft rolling and also have a thrust to CN1 table. I concluded that the sim1.DLL values are approximately treble the real world values for concrete (0.014).
Its not just the rolling friction coefficients, the sliding is wrong also which is why aircraft skid in turns whilst taxiing.
The problem for LM here is that if they fix sim1.dll, they break every other legacy airfile. Its not a big job to fix the airfile, but I suspect commercial developers would rebel against this !
Re: Ground surface friction
This is already posible via PDK by using custom simulation, environment forces and subsystems factories.
Regards,
Simbol
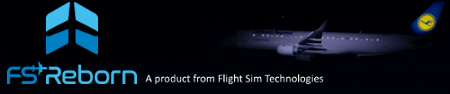
CEO Flight Sim Technologies Ltd
Oficial Website: https://www.FSReborn.com
Re: Ground surface friction
I hope LM and the developers can rewrite the airfiles as it is needed. Please LM fix the SIM1.DLL as outlined above. Skidding whilst taxiing is not fun or realistic for training.kand wrote: The original default values contained in SIM1.DLL are the issue, I have done a lot of research on friction coefficients and posted my findings on fsdev. The bottom line here is that using the default rolling friction sim value for concrete causes other values within the airfile to become skewed. All of the airfiles available today are made to overcome this incorrect value with side effects.
The high default rolling friction value causes the turbine tables to be skewed to overcome high friction, one must set high Fn (net thrust) in 1506 for the idle/static mach line. This higher unrealistic Fn value causes fuel burn to be higher at idle because FB is proportional to thrust. Some developers then overcome this high FB part by faking the fuel burn gauge to display the correct FB bypassing the sim variables.
I have experimented a lot here and set up an airfiles turbine tables to exactly match the real GE90-94b. I know the thrust values (at ISA and ZFWs) to get the aircraft rolling and also have a thrust to CN1 table. I concluded that the sim1.DLL values are approximately treble the real world values for concrete (0.014).
Its not just the rolling friction coefficients, the sliding is wrong also which is why aircraft skid in turns whilst taxiing.
The problem for LM here is that if they fix sim1.dll, they break every other legacy airfile. Its not a big job to fix the airfile, but I suspect commercial developers would rebel against this !
SIMBOl - I realise that custom simulation is available but it still does not seem to be a solution for realistic high fidelity flight modelling. Aircraft still fly "on rails" PMDG and FSL do a better job but even those models are not where they could be if LM improved the modelling.
Blessings
Duncan Odgers
Re: Ground surface friction
funkyaz77 wrote: ↑Thu Apr 25, 2019 3:17 pm
SIMBOl - I realise that custom simulation is available but it still does not seem to be a solution for realistic high fidelity flight modelling. Aircraft still fly "on rails" PMDG and FSL do a better job but even those models are not where they could be if LM improved the modelling.
Blessings
Duncan Odgers
Duncan,
This is not the case, the way the PDK Simulation service works, is that it allows to Implement and override "Anything" during the simulation implementation, this means developers could literally create a Plugin that implements custom flight system as desired for all flyable objects inside P3D.
I have done many experiments with it, and for example you can simulate perfectly the forces that occur when an engine failure happens to a propeller during take off or during flight, runway wet surfaces skids, etc. The only limit is the developer imagination.
Although PMDG, Majestic Q400 and FSL are using custom flight models that are very good, they are not using the PDK:Isimulation plugin at this stage, however if they were, I am 1000% confident that their simulation model would become even more accurate given the capabilities of the P3D PDK Libraries, however their products would not work anymore for FSX as they would need to become an exclusively product for P3D only :wink.
Regards,
Simbol
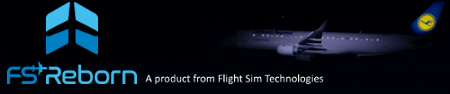
CEO Flight Sim Technologies Ltd
Oficial Website: https://www.FSReborn.com
Re: Ground surface friction
Simbol,
Thank you for taking the time to explain, maybe a feature should be then to get LM to restrict developers to only use the PDK so they cannot keep developing for FSX which is an entertainment product. Developers have been lazy and not all have fully explored the P3D V4 PDK which as you have explained is very powerful and allows for every type of flight model. Once people start developing for P3D only then I think thats when we will see the advancements in the sim.
A feature should also be that all developers are forced to use the LM install method hence navigating most of the add on complexity.
Blessings
Duncan
Thank you for taking the time to explain, maybe a feature should be then to get LM to restrict developers to only use the PDK so they cannot keep developing for FSX which is an entertainment product. Developers have been lazy and not all have fully explored the P3D V4 PDK which as you have explained is very powerful and allows for every type of flight model. Once people start developing for P3D only then I think thats when we will see the advancements in the sim.
A feature should also be that all developers are forced to use the LM install method hence navigating most of the add on complexity.
Blessings
Duncan